Interarch Delivered Greenfield Manufacturing Unit with World Class Safety for Asian Paints Ltd in Karnataka
|
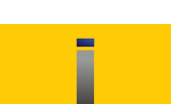 |
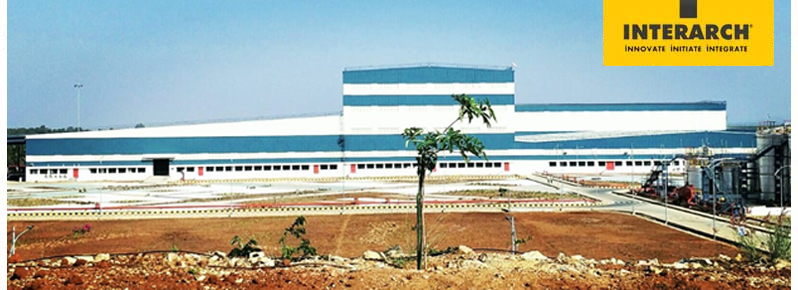 |
|
|
Asian Paints Ltd is an Indian multinational paint company headquartered in Mumbai, Maharashtra. The Company is engaged in the business of manufacturing, selling and distribution of paints, coatings, products related to home decor, bath fittings and providing related services. Asian Paints is India's largest and Asia's third largest paints corporation.
Asian Paints decided to set up a new facility in Mysore using the most advanced construction materials and methods, and as per International standards. The newly commenced paint manufacturing plant in Mysore district, in the state of Karnataka, is towards fulfilling the long term capacity requirements of the Company and is subject to the future demanding conditions.
|
|
|
|
Scope of Work |
|
Asian Paints opted for Interarch an obvious choice given global recognition for commitment towards World-class safety standards & time bound execution of the project. Interarch Pre Engineered building system for Asian Paints gives the building a global edge in terms of durability, protection and design.
Interarch had successfully executed their Greenfield paint manufacturing facility 20 buildings in the project area spread over 57,000 Sq. M consisting manufacturing plant, Material storage & other utility building.
|
|
|
|
Design Expertise |
|
The building design was complex in nature on aspects of the high, low bay frame along the length. With building connected to the adjacent building along the side wall. A High bay area having a clear span of 48.6 M and 26 M clear height made design and detailing challenges.
Leak proof arrangement at the junction between high bay and adjacent building over 103 M with gable end was a big challenge. The future expansion provided on sidewall throughout the length, which was a challenge to design for the provision of present and future scope.
The building had to be designed using the latest Indian standard through Staad 3D model. Dead and live load are designed as per IS: 875 (Part 2), Wind load is designed as per IS: 875(Part 3), Seismic load is designed as per IS: 1893-2002 and Design deflection as per IS: 800-2007. Collateral loads of Solar panel, Utilities and Cable trays considered from the roof.
|
|
|
|
|
Aesthetic & Comfort Feature |
|
For Aesthetical feature, Sheeting Color pattern has also considered for an attractive look. The ventilation system was provided on the roof and wall as an effective and environment friendly solution to meet the building’s natural ventilation requirement.
GI Box gutter with Header pipe system was considered to prevent drainage water dispose over the adjacent building roof. The building is provided with a lean-to building with full-length jack portal over 18 M length to facilitate vehicle loading & unloading added the aesthetic feature. Single skin insulation on the roof and daylight panel is provided on the roof
|
|
|
|
Project On-Site Management |
|
Our dedicated project teams regularly evaluate the site management plan and follow strictly and take immediate action in case of any rectification as per requirement. To achieve Zero accident practice, proper safety measures prescribed by Indian codes and standards have been adopted and monitored through the project head at the site and Head office. Site Incharge needs to sign-off a safety declaration form regularly before starting to work. |
|
|
|
|
Safety Measures adopted |
Following measures are taken from our side to ensure Zero Accident policy- |
 |
Provided require PPE according to Job criteria. |
 |
 |
Daily checking of workers for a gate pass, mobile phones, smoking items & tobacco, etc |
 |
Hard barricades around the DG & panel boards |
 |
Using Standard scaffolding & platform for profiling machine |
 |
Routine checking of Ambulance & toilet |
 |
Ensure all labours are medically fit to get a medical fitness certificate from MBBS doctors. |
 |
Fobia test arrange at the site for height work. |
 |
Induction training provided to all, whoever working at the site. |
 |
All vehicle Inspection before to start work. |
 |
All Tools & Tackles Inspection before to use at the site. |
 |
Ensure Access availability for height work as well as for the working area. |
 |
Inspections of Electrical equipment & Portable tools. |
 |
Safety static report weekly & monthly maintained at the site. |
 |
Training & Motivation program arrange at the site on a weekly basis. |
 |
Mock drill on a quarterly basis provided. |
 |
Lifeline test arranges at the site. |
 |
Windsock provided to show wind directions helpful for sheet shifting work. |
 |
For each and every Tools & Machinery getting TPI at the site level. |
 |
Proper material stacking according to the logistic plan submitted. |
 |
We maintain Safety manual, HSE policy & EHS plan at the site. |
 |
Maintain Emergency plan & Logistic plan on site. |
 |
Safety observation & compliance report. |
 |
Maintain all Safety check list at the site. |
 |
Provided store for tools & tackles as well as Safety Park, assembly point. |
 |
The emergency vehicle provided permanently. (Ambulance). |
 |
First aid Room & Induction room maintained at the site. |
 |
Proper scrap yard provided. |
 |
At every working location, we are arranging a safety person with a supervisor. |
 |
|
|
|
Difficulties faced & Solution provided during Execution |
|
Execution of a building at a height above 26 M considering all safety measures was a big challenge for the project team and the site was also at remote locations, machinery and tools were mobilized from 200 km away from the site.
In the mid of execution, the client has changed some specifications of the building for which site modification is done under prior supervision and time and resource loss.
|
|
|
|
Multiple contractors were working at a particular job location due to which front availability and synchronization problem arises between the contractors and to overcome we discuss the matter with Client and adequate measure taken. Each and every activity mocks should be provided by the project manager and periodic inspection of the roof to ensure the quality of work.
All machines & tools were strictly inspected by an Interarch safety team on a regular basis to ensure safety. Due to the building height of 26 M, we ensure Boom lift and Lifeline safety system, Safety belts and other safety measures for workers working at height.
One major challenge was to paint fading of the structure during rain and we have done the cleaning and repaint the structure which leads to time consuming and cost addition.
|
|
|
|
|
|
Outcome |
|
The outcome of our consolidated efforts was a successful delivery of the Asian Paints Ltd project with best-in-class products and construction methodologies. Teamwork, collaboration, an effective planning methodology were the main catalysts for completion of the project. |
|
|
|
|
|
© Copyright 2010, all rights reserved with Interarch Building Products Pvt. Ltd.
visit us at: www.interarchbuildings.com, www.interarchinfra.com |
 |